印制电路板的基本要求
- 发布时间: 2021-06-30
印制电路板的基本要求
- 发布时间:2021-06-30
详情
一.印制基板的基本功能
1.足够的机械强度;
2.能够承受组装工艺中的热处理和冲击;
3.具有足够的平整度以适应自动化的组装工艺;
4.能承受 6 次以上的焊接和返修工作;
5.良好的电气性能和耐潮湿性能;
6.良好的尺寸稳定性。
二.印制电路板性能等级
军用印制电路板性能等级分为如下三级:
1级:普通军用电子设备,主要用于地面和一般军用设备。要求印制电路板组装后有完整的功能,一定的工作寿命和可靠性,允许有一些不影响电气和机械性能的外观缺陷;
2级:专用军用电子设备,主要用于军用通信设备、复杂的军用电子设备等。要求印制电路板组装后有完整的功能,较长的工作寿命及较高的可靠性,允许有不影响使用性能的轻微外观缺陷;
3级:高可靠军用电子设备,主要用于车载、机载、舰载、航天等军用电子设备。要求印制电路板组装后有完整的功能、长的工作寿命、连续工作和高的可靠性,在使用中不允许发生任何故障。
三.印制电路板基本要求
1.印制电路板应符合设计文件和工艺文件要求,根据印制板结构确定基材的覆铜箔面数(单面、双面或多层板),并与组装过程中选用的元器件、工艺材料的特性相兼容。
2.印制电路板外观要求
1)基板面应平整、边缘整齐、图形不失真;不应有碎裂、毛刺、起泡和分层 ;
2)印制导线表面应光洁,色泽应均匀,无翘箔、鼓胀和明显的划痕;
3)表面镀层应光亮均匀,不起皮鼓泡;
4)阻焊膜厚度应不大于焊盘的厚度;
5)焊盘上应无字符、阻焊膜和其它污物沾污;
6)其它性能应符合GJB362B中的有关要求。
3.印制电路板应适用于波峰焊和再流焊。
4.平整度(弓曲和扭曲)
焊接前通孔插装PCB的弓曲和扭曲应不大于1%,表面安装用PCB的弓曲和翘曲一般应不大于 0.75%,窄间距应不大于 0.5%。
5.工艺基准孔、识别标志及焊区的安装位置精度应符合组装工艺要求,标志表面平整、无沾污、亮度均匀,相对背景有较高的反差。
6.印制电路板表面涂(镀)覆层的选择
1)军用PCB 表面涂(镀)覆层应采用热风整平工艺或电镀镍金工艺,不应使用化学镀镍金工艺;PCB 表面涂(镀)覆层应在PCB 装配图上注明。
2)PCB 焊盘及金属化通孔可焊性保护层应采用含铅量≥3%的铅锡合金焊料;表面安装焊盘采用锡铅合金为可焊性保护层,锡铅合金层厚度应不小于 2.8μm~8μm。对于 3 级印制电路板和高密度PCB 建议使用电镀镍金(Ni/Au)为可焊性保护层。Ni层为 5μm~7μm,Au层为 0.05μm~0.15μm。
3)阻焊膜的涂覆按 GJB362B的 3.5.1.8执行。固化的阻焊膜的最小厚度按GJB4057的规定,2级板为 10μm,3级板为 18μm;
4)需要安装(螺装或焊接)屏蔽盒的印制表面涂覆铅锡焊料时,应尽量减少铅锡焊料涂覆面积,或按进行阻焊膜与镀锡层交叉的网格方式设计大面积接地面。
7.印制电路板的可焊性
1)印制电路板金属化孔的可焊性
按QJ832A 规定的试验后,焊料应润湿到孔顶部周围的焊盘(连接盘) 上。在焊接温度为 232℃~237℃,焊接时间为 3s 的条件下,金属镀层应对焊料呈湿润状态,必须完全润湿孔壁,不应有不润湿或露基底金属的现象。 可不完全填满孔,但焊料相对于孔壁的接触角应小于90º。
2)印制电路板表面可焊性
根据规定的焊接温度、焊接时间和附着在导体上焊料层的外观,表面可焊性要求按表 4 规定。
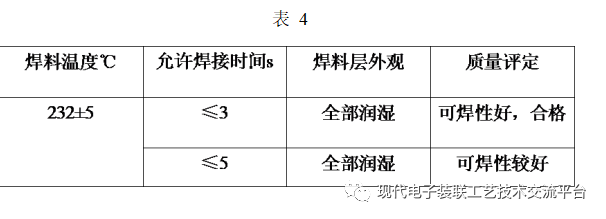
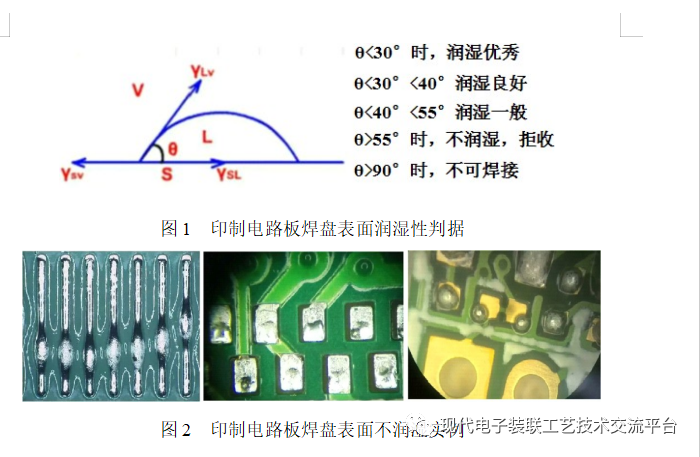
8.印制电路板的耐热性(热应力)
1.印制电路板在温度 287℃±6℃的熔融焊料中浸焊 10s~11s 后,不应出现分层、起泡或破坏,表层印制导线对基板的抗剥强度应符合抗剥强度的要求,阻焊层不出现起皱、脱落等现象。在实际焊接过程中,印制电路板元器件和导线的手工焊接温度规定为240℃±10℃,波峰焊焊接温度为250℃±5℃,再流焊焊接温度为235℃±5℃;按上述规定执行时,如印制电路板出现分层、起泡、或破坏,或阻焊层不出现出现起皱、脱落等现象则是印制电路板的耐热性(热应力)不符合要求。
9.阻燃型环氧树脂纺织玻璃布基材(FR-4)抗剥强度
1.在正常条件下厚度 35μm以上的FR4基板表层印制导线对基板的抗剥强度应不小于 1.4N/mm;厚度为 18μm的FR4基板表层印制导线对基板所承受的最小剥离强度应不小于 1.1N/mm;在经受 2)规定的试验条件后, FR4 基板多层印制电路板表层印制导线对基板的抗剥强度应不小于1.2N/mm。
2)在下列条件下连续依此放置后,FR4基板表层的印制导线对基板的抗剥强度应不小于 1.2N/mm。温度-65±2℃下放置 6h;温度 125±2℃下放置 16h;在交变湿热条件下放置 48h。10.PCB 基材选用设计时应根据PCB 的使用条件和机械、电气性能要求选择基材:
1)根据印制板的尺寸、单位面积承载元器件质量,确定基材板的厚度;
2)选择时还应考虑到电气性能要求、Tg和CTE、平整度等因素及孔金属化的能力;
3)除设计另有规定外,印制板所用的基材为阻燃型环氧树脂纺织玻璃布基材(FR- 4)
四.混装印制电路板
1.混装印制电路板基材要求
有铅元器件和无铅元器件混装PCB 基板材料主要根据电子产品的性能指标、使用环境、焊接温度来选择。
1)焊接温度 240℃以下的产品,采用FR4 环氧玻璃纤维基板;
2)焊接温度 240℃~250℃的产品,可选择高 Tg 为 150℃~170℃的FR-4;
3)高可靠及厚板,焊接温度 250℃以上的产品,采用FR-5;
4)使用环境温度较高或挠性电路板采用聚酰亚胺玻璃纤维基板;5)对于散热要求高的高可靠电路板采用金属基板;
6)对于高频电路则需要采用聚四氟乙烯玻璃纤维基板。
1.混装印制电路板焊盘表面镀(涂)层
应选择可焊性符合GJB362B 要求的印制电路板表面镀层,同时应考虑成本、储存条件等因素。高可靠军用电子设备推荐采用Pb-Sn 热风整平(HASL)镀层。
如果产品对于焊盘的平整度有较高的要求,推荐采用电镀 Ni/Au 镀层。高密度组装建议采用电镀 Ni/Au 镀层,备选Pb-Sn 热风整平(HASL)镀(涂)层。
有些军品PCB表面镀层的设计中为了满足两次回流焊的需求,避免二次回流焊时,第一次焊接的元器件掉件,采用“温度阶梯焊”工艺,即 PCB 的A面热风整平Pb-Sn合金镀层,而在 B面涂覆无铅焊料,这是不可取的 ; 掉件问题可以通过PCB布局设计解决,也可以通过其它工艺方法解决。1)设计方法采用双面再流焊的混装时,印制电路板设计应将大元器件布放在A面,小元器件在B面。

放置在B面的元器件应遵循以下原则:元器件(Dg)/焊盘面积<30g/in2式中:
Dg—元件质量;
P—该元件焊盘总面积。
双面再流焊工艺一般先焊B 面,然后再焊 A 面,如果辅 B 面的元器件质量过重,二次回流时可能落在再流焊炉中。
当质量/面积比(Dg/P)小于 30g/in2 时双面再流焊二次回流,元器件也不会掉下来。
2)工艺方法
(1)第二次再流焊时将再流焊炉上/下温区设置一定的温度差,一般炉子底部温度低于顶部温度 20℃~30℃。
(2)采用胶粘剂:B面的SMD/SMC经过两次再流焊。当A面焊接时,B 面向下,已经焊在 B面的元器件在A面再流焊时,其焊料会再熔融,而且较大的元器件在传送带轻微振动时回发生偏移,甚至脱落,所以涂覆焊膏前还需用胶粘剂固定。
五.层压板白斑和微裂纹等质量要求
1.IPC-610E-213
这种固有的层压板状况是在印制板制造或组装过程中造成的。组装过程中引起的白斑和微裂纹(例如:插针的压接,再流焊等),通常不会进一步扩展。白斑违反最小电气间隙的情况下,考虑到产品的运行环境条件,例如潮湿环境、低气压等,可能需要进行额外的性能测试和电介质阻抗测量。基板内含埋入式元器件的场合,可能需要规定另外的要求。
1.1白斑
1.1.1定义:一种发生在层压基材内部,玻璃纤维在编织交叉处与树脂分离的情形,表现为在基材表面下分散的白色斑点或“十字纹”,通常和热应力 有关。
1.1.2合格1,2,3级:无白斑迹象。
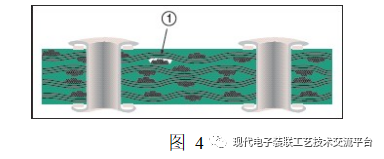
1.1.3可接受1,2级
1)对白斑的要求是组件功能正常。
制程警示3级:层压基板内的白斑区域超过内层导体间物理间距的50%。
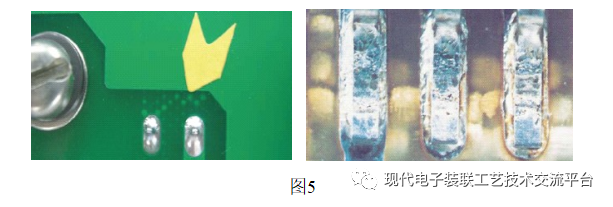
注:白斑不是缺陷条件。白斑是在热应力下可能不会蔓延的内部状况, 且目前尚无定论证明白斑是导电阳极丝CAF生长的催化剂。分层是在热应力下可能蔓延的内部状况,且可能是CAF生长的催化剂。IPC-9691耐CAF 测试用户指南和IPC-TM-650测试方法2.6.25提供了确定与CAF生长有关的层压版性能的更多信息。
1.1微裂纹
1.1.1定义:一种发生在层压基材内部,玻璃纤维在编织交叉处与树脂分离的情形,表现为在基材表面下连续的白色斑点或“十字纹”,通常和机械应 力有关。
1.1.2合格1,2,3级:无微裂纹迹象。
1.1.3可接受
1)1级:对微裂纹的要求是组件功能正常。
2)2,3级
(1)层压基板内的微裂纹区域不超过非公共导体间物理距离的50%。
(2)微裂纹未使间距减少到最小电气间隙以下。
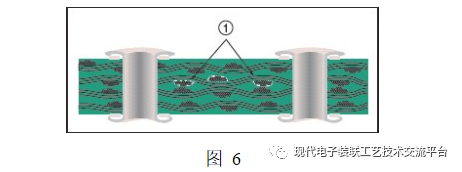
1.2.4缺陷- 2,3级
1)层压基板内的微裂纹区域超过非公共导体间物理距离的50%。
2)间距减到最小电气间隙以下。
3)板边缘处的微裂纹使导电图形到板边的距离减到最小距离以下,或无具体规定时,减少量大于2.5mm。
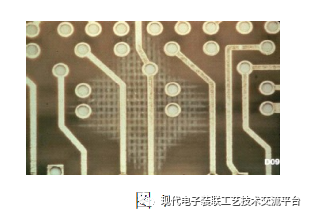
1.1起泡和分层
一般情况下,分层和起泡是因材料或工艺存在先天不足造成的。对于发生在功能区与非功能区之间的起泡和分层,只要是绝缘的,并且其它要求都满足,可以是可接受的。
1.1.1定义
1)起泡:一种表现为层压基材的任何层与层之间,或基材与导电箔或保护 性涂层之间的局部膨胀与分离的分层形式。
2)分层:印制板内基材的层间、基材与导电箔间或任何其他面间的分离。
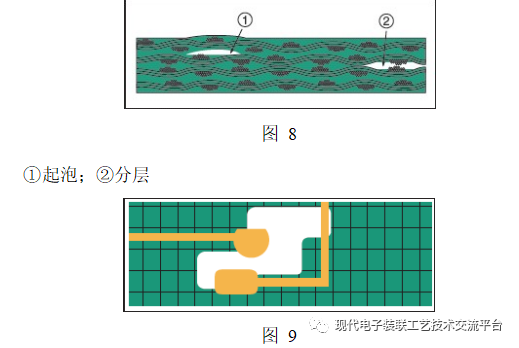
1.1.1合格1,2,3级:无起泡或分层。
1.1.2可接受- 1,2,3级:起泡/分层范围未超过镀覆孔间或内层导体间距离的25%。

1.3.4缺陷:1,2,3级
1)起泡/分层范围超过镀通孔间或内层导体间距离的25%。
2)起泡/分层使导电图形间距减少至最小电气间隙以下。
注:起泡或分层范围可能在组装或运行期间增加。这时可能需要制定单独的要求。
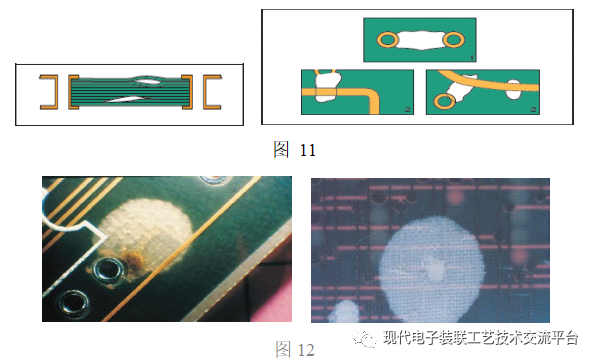
1.1显布纹/露织物
1.1.1定义
1显布纹定义:基材表面的一种状况,虽然未断裂的纤维完全被树脂覆盖 , 但显现出玻璃布的编织花纹。
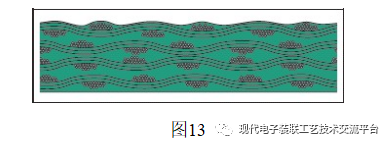
1)露织物定义:基材表面的一种状况,未断裂的编织玻璃布纤维没有完全被树脂覆盖。
1.1.1显布纹可接受1,2,3级:显布纹对于所有级别都可接受,但因其与露 织物相似的表面特征而很容易与之混淆。注:可用显微剖切图片作为显布纹的佐证。
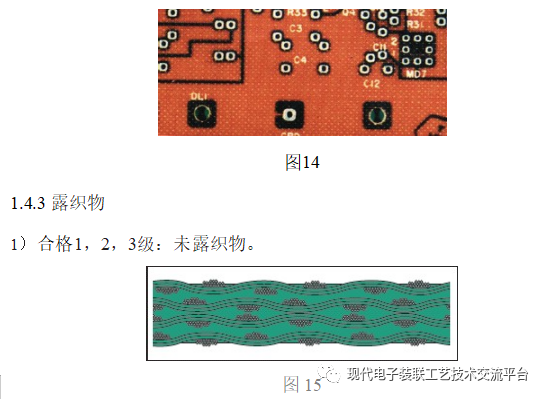
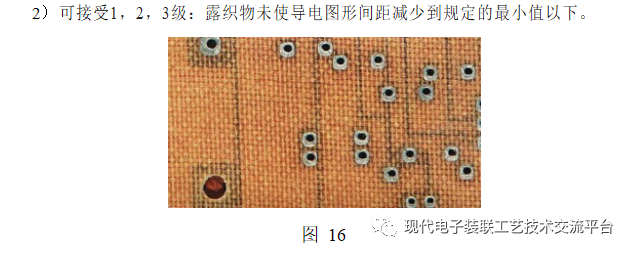
3)缺陷
(1)2,3级:表面损伤切入层压板纤维。
(2)缺陷1,2,3级:露织物使导电图形间距减小至最小电气间隙以下。
2.IPC-6012C-2010
1)白斑
对于 1 级、2 级和 3 级产品,白斑都是可接受的。层压板板基板中白斑面积大于相邻导体间距的 50%时,对于 3 级产品是一种制程警示,说明材料、设备操作、工艺或制程出现变异,但不是缺陷。虽然应该将制程警示作为过程控制系统的一部分进行监控,但不要求对个别制程警示进行处置。且受影响产品应照常使用。
注:白斑是层压板中的一种内部现象,再热应力作用下它可能不会扩展,同时也无明确结论显示它是导电阳极丝(CAF)生长的诱因。分层是一种在热应力作用下可能扩展的内部现象,同时也可能是 CAF 生长的诱因。关于耐CAF 测试,IPC-9691 用户指南和IPC-TM-650 测试方法 2.6.25 均提供了确定层压板CAF 生长性能的其他信息。
2)微裂纹
如果微裂纹不会使导体间距减小至低于最小值,且没有因为模拟组装过程的热测试而扩大,则对于所有级别产品均是可接受的。对于 2 级和 3 级产品,微裂纹的跨距不应当超过相邻导体间距的 50%。
3)分层/起泡
如分层和起泡影响的区域未超过印制板每面面积的 1%,且其未使导电图形的间距减小至低于最小导体间距,则对于所有级别产品均是可接受的。经过模拟组装过程的热测试之后,分层和起泡应当没有扩大。对于 2 级和 3 级产品,分层/起泡的跨距不应当大于相邻导电图形间距的 25%。
3.GJB4896-2003
1)白斑
按下列要求判定:1、2、3级板接收状况(见图17):除用于高电压产品外,白斑均可接收。
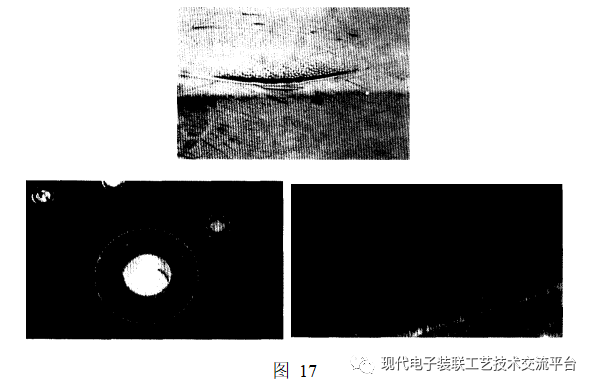
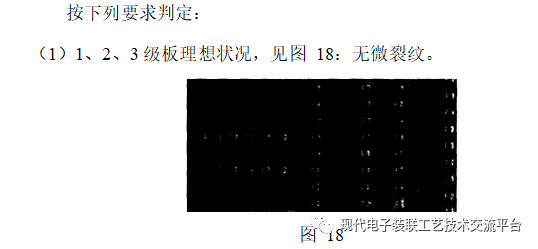
(2)1、2、3 级板接收状况:
①1 、 2 、 3 级 板
a)缺陷未使导电图形的间距减小低于最小导线间距。
b)经热应力试验后缺陷不扩大。
c)板边缘的微裂纹不使板边缘与导线的间距减小到低于规定的最小值:若未规定最小值,则间距应大于 2.5mm。
②2、3 级板,见图 19:微裂纹区域不超过相邻导线间距的 50%。
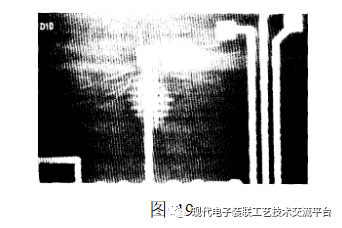
③1 级板,见图 20:微裂纹区域超过相邻导线间距的 50%,但不使相邻导线间产生桥接。
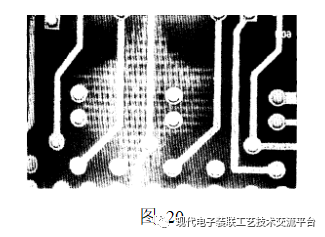
(3)1、2、3 级板拒收状况:缺陷超过上述情况。
3)分层/起泡
按下列要求判定:
(1)1、2、3 级板理想状况,见图 21:无分层和起泡。
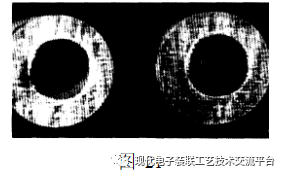
(2)可接收状况,见图 22:
①1 、 2 、 3 级 板
a)每面受缺陷影响的面积不大于板面积的1%;
b)缺陷与最近导体的距离满足规定的最小间距要求;
c)缺陷经过热应力、模拟返工或热冲击试验后不扩大;
d)缺陷与板边的距离大于规定的最小值;若无规定,则大于 2.5mm;
e)由于增强粘接处理面出现的铜箔表面变色或杂斑现象。
②2、3 级板:
a)在相邻导体或镀覆孔之间的起泡或分层,不大于其间距的 25%; b)任何孤立缺陷的最大尺寸不大于 0.80mm;在非导电区域,缺陷的最大尺寸不大于 2mm 或印制板面积的 1%。
③1 级板
缺陷在导体之间,并大于其间距的 25%,但未在道题之间产生桥接。
(3)1、2、3 级板拒收状况缺陷超过上述规定。
注:受影响的面积是由各缺陷面积的总和除以印制板的总面积来确定的。每面应单独测量。
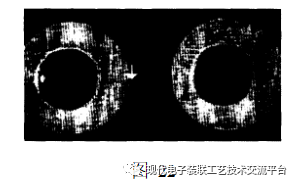
4.GJB362B-2009对白斑和微裂纹等的质量要求
1)斑点
理想情况下应无斑点。斑点若属于下列情况可以接收:
(1)斑点是半透明的;
(2)斑点是显布纹,而不是分层或分离
(3)孤立的斑点离导线的距离不小于 0.25mm。或经过任何焊接操作后不扩大(凝胶颗粒不管在任何位置均可以接收)。
2)白斑和裂纹
理想情况下应无白斑和裂纹。若属于下列情况可以接收:
(1)若印制板不用于高电场,则白斑可接收;但白斑总面积应不大于印制板总面积的2%(两面计算),任何方向的尺寸应不大于0.80mm;且不使相邻导电图形之间桥接;
(2)裂纹未使导电图形的间距减小到低于布设总图中规定的最小值;
(3)热应力试验后裂纹不扩大;
(4)板边缘的裂纹不应使板边缘与导线的间距减小到低于布设总图中规定的最小值;若未规定最小值,则间距的减小应不大于 2.5mm;
(5)裂纹不应超过相邻导线间距的 50%。
5.QJ831B-2011对白斑和微裂纹等的质量要求
1)白斑和裂纹
如果不用于高电场,多层板上的白斑和裂纹应不大于多层板总面积的2%,在内层导线间,应不大于该处间距的 25%,在任何方向上的尺寸应不大于 0.8mm。
2)表面下斑点表面下斑点符合下列条件时,应判为合格:
(1)当表面下斑点是半透明的,或确知为显露布纹而不是分层和分离;
(2)孤立的斑点距导线的距离至少 0.25mm;
(3)经过任何焊接操作后不扩大
结束语 为提高产品设计和组装焊接质量,实施可制造性设计和工艺过程控制是必不可少的。《高可靠印制电路板可接受条件》就是高可靠 PCBA 组装焊接的前提。
我们应立足预防为主,在设计阶段就对不同等级 PCB 的可接受条件作出明确规定,其中包括PCB 的验收要求;例如军品可以按照GJB362B 的规定进行PCB 的验收,这样就可以控制PCB 供货的质量源头。
在此基础上,强化PCBA 组装焊接工艺控制,就可以避免类似白斑、微裂纹、分层和起泡等质量问题的出现。
业内人士往往注重于各类分析,例如案例分析、质量分析、可靠性分析和缺陷分析等;这是不可少的,但总体上属于“事后诸葛亮”。
各类分析的最终目的不是就事论事,而是要落实到预防为主的措施上来,这就是前面提到过的可制造性设计和工艺过程控制。
如果我们的印制板是按照GJB362B 验收的,就可以排除PCB 货源的问题。在组装焊接中出现“白斑”的原因基本上是焊接温度过高,例如军品焊接无铅BGA 时峰值温度要达到 240℃,或手工焊接时实际焊接温度过高,焊接时间过长,PCB 的玻璃化转化温度过低等,需要引起我们的注意 。
转载:现代电子装联工艺技术交源平台
详情
据国外媒体报道,韩国是全球率先推出5G商用服务的国家,他们在2019年的4月3日就推出了5G商用服务,目前5G在韩国商用已超过两年。
同其他推出5G商用服务的国家一样,韩国5G商用网络的覆盖范围还在不断扩大,5G用户也还在不断增加之中,不过在用户规模上尚未占据主导地位。
韩国媒体援引韩国科学和信息通信技术部的数据报道称,自2019年推出5G商用服务至今,他们的5G商用网络已覆盖85座城市。
在5G用户规模方面,韩国科学和信息通信技术部的数据显示,到7月底,韩国5G用户就已达到了1708万,当月新增61.6万。
5G用户数量持续增加,5G用户在韩国移动通信用户中所占的比例,也在不断提升,到7月底,韩国移动通信用户共有7171万,5G所占的比重,已经提升到了约24%。
随着更多5G智能手机的推出和5G网络覆盖范围的扩大,韩国5G用户的数量也将不断增加,韩国媒体在报道中就表示,在下半年新推出的5G智能手机的推动下,预计5G用户规模的增长速度在今年年底将加快。
扫二维码用手机看
上一个:
无
上一个:
无
杭州景皇电子科技有限公司 版权所有 Copyright©2024 All Rights Reserved 浙ICP备2024087502号